Non-aseptic powder and liquid filling machines
LF Series for liquid filling and capping
Efficient solution for filling of non-aseptic pharmaceutical and nutraceutical liquid products into a wide range of glass and plastic bottles. The machines can be equipped with up to three capping stations plus a straw/cannula feeding unit.
From sugary, highly viscous products, such as syrups, to alcohol-based, low viscosity products, within the same machine configuration.
Multiple caps handling – screw caps, child-proof caps, droppers, spray pumps, measuring caps and more.
Reliable solution for continuous production of big batches.
- Up to 15,000 bottles/hour.
- Can be fitted with up to three capping stations plus straw handling unit.
- Can be equipped with volumetric pumps for mass-flow dosing system.
- Format-free linear transport in the filling area.
- Nitrogen flushing into the bottles for oxygen sensitive products.
LVI Series for liquid filling
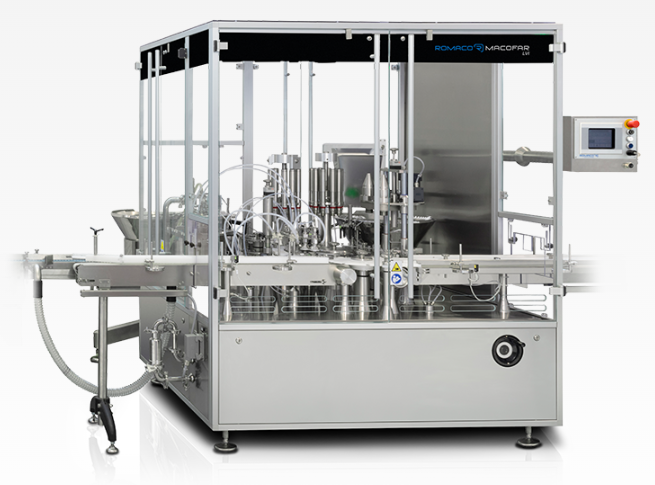
Sterile and non-sterile liquid filling and capping. Compact versatility for complex products: LVI machines can be equipped with different types of liquid filling technologies and capping options. Suitable to handle a wide range of pharmaceutical liquid products. The machine can also be equipped with laminar flow and environmental controls for aseptic processes. Unit can handle injectable, ophthalmic, oral and nasal products.
- Up to 6,000 bottles/hour.
- Torque control on capping unit.
- Nitrogen flushing.
- Up to two double capping stations inside the machine body.
- Downstream C.W. integration.
- Viable and non-viable particles monitoring.
- Compact design.
MACRO Series for powder filling and capping
Non-sterile powder filling and capping. High accuracy filling of non-free flowing powders and dry syrups into glass or plastic bottles. Closing unit can be customised to handle any type of cap. Reliable technology for precise powder filling in non-aseptic operations.
Glass partition wall separating the closing station from the filling station to avoid particle contamination of the bottles. Individually configurable pistons and stainless steel wire mesh filters according to powder’s physical properties. Multiple filling into one bottle to increase the dosing range available upon demad. System is also available without the closing group.
- Up to 8,000 bottles/hour.
- User friendly 15'' touchscreen HMI.
- Vacuum-pressure dosing disk.
- Bottles transport, dosing carousel and vibrating unit.
- Torque control on capping unit.